Services
Wyampa Heat Treatment is able to offer services to Australian We are committed to delivering fast and on time jobs to you. We offer in house transport for customers in the Brisbane area.
Heat treating Aluminum
The application of the term heat treatable to aluminum alloys, both wrought and cast, is restricted to the specific operations employed to increase strength and hardness by precipitation hardening thus the term heat treatable serves to distinguish the heat treatable alloys from those alloys in which no significant strength improvement can be achieved by heating and cooling. The non-heat treatable alloys depend primarily on cold work to increase strength.
This is applicable to the heat treatable alloys and involves a heat treatment process whereby the alloying constituents are taken into solution and retained by rapid quenching. Subsequent heat treatment at tower temperatures i.e. ageing or natural ageing at room temperature allows for a controlled precipitation of the constituents thereby achieving increased hardness and strength.
Time at temperature for solution treatment depends on the type of alloy and the furnace load. Sufficient time must be allowed to take the alloys into solution if optimum properties are to be obtained.
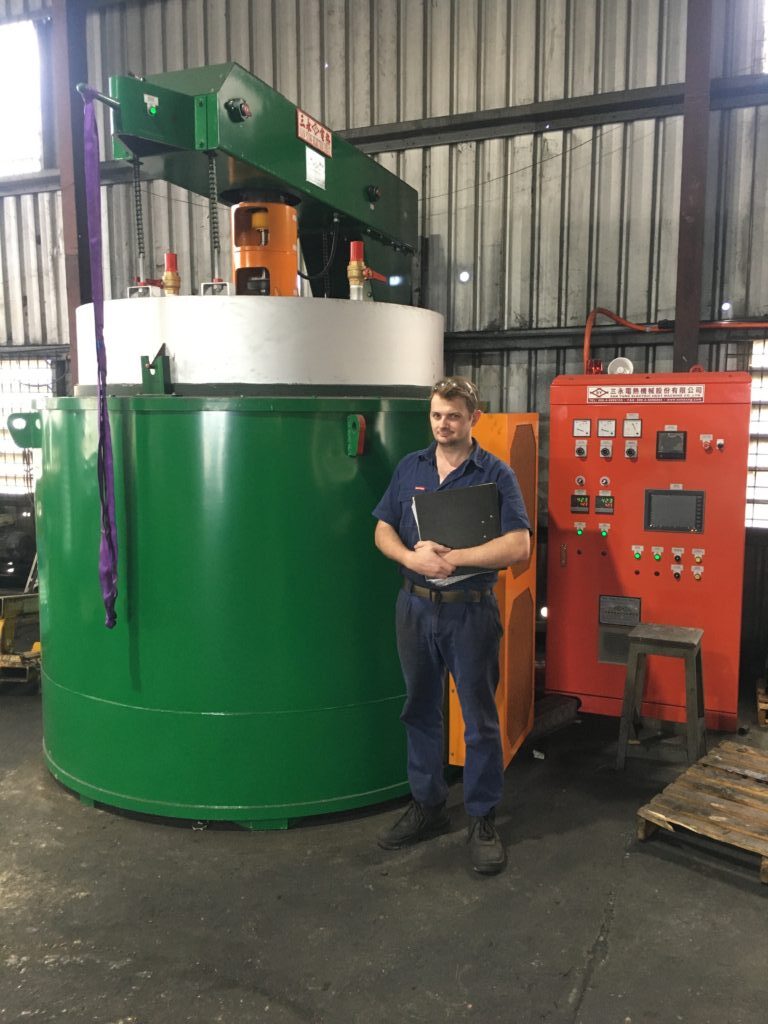
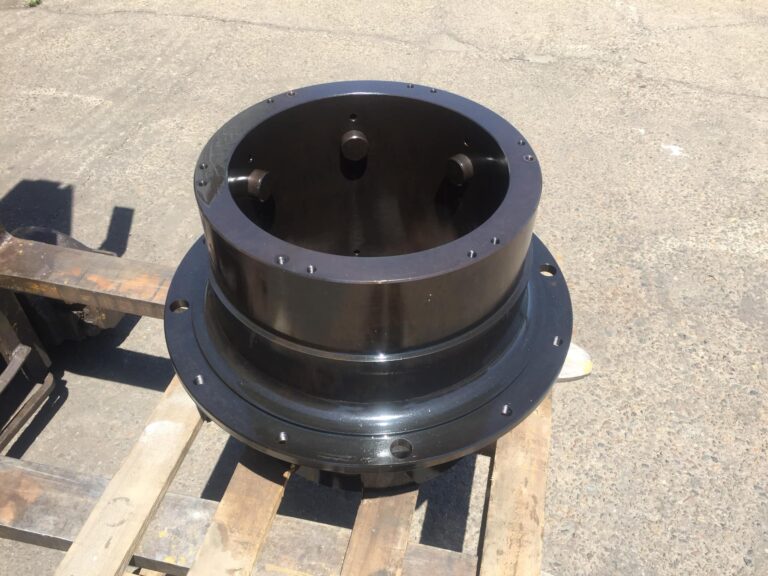
ANNEALING NORMALIZING AND STRESS RELIEVING
The primary purpose of an annealing treatment is to reduce the hardness of a material and facilitate the progress of subsequent manufacturing operations.
Annealing is commonly used after casting, forging or rolling to soften materials and minimise residual stresses, improve machinability, and increase
ductility by carefully controlling the microstructure. Many steels in strip form are annealed, as are most tool steels and stainless steels.
Non-ferrous alloys are also annealed.
NITRIDE TUFFTRIDE
The Tufftride process of Durferrit is a surface heat treatment Salt Bath Nitrocarburizing treatment carried out at around 580°C for relatively short times (30 minutes to 3 hours) which produces a hard wear resistant surface on many steels. In this type of surface heat treatment It is common to oxidise the surface compound layer formed, by using the oxidising AB1 salt bath. Corrosion resistance of the steel is enhanced by formation of this surface layer in a similar way to many other Nitrocarburizing treatments. Fatigue strength and indentation resistance is superior to untreated steel due to a diffusion layer beneath the compound layer. The depth of this diffusion layer depends on the time of the Tufftride® treatment and the type of steel being treated.
This treatment is used as an alternative to chrome or nickel plating.
Benefits of Tufftriding:
- Increased surface hardness
- Improved fatigue strength
- Increase in corrosion resistance
- Increased wear resistance
- Reduces scuffing
If choosing a Tufftriding treatment, consideration must be given to component geometry, particularly blind threaded holes.


Harden and Tempering
Hardening and tempering of engineering steels is performed to provide components with mechanical properties suitable for their intended service. Steels are heated to their appropriate hardening temperature {usually between 800-900°C), held at temperature, then “quenched” (rapidly cooled), often in oil or water. This is followed by tempering (a soak at a lower temperature) which develops the final mechanical properties and relieves stresses. The actual conditions used for all three steps are determined by steel composition, component size and the properties required.
Two specialised quenching options can be applied in special circumstances: Martempering (also known as “marquenching”) uses an elevated-temperature quench (in molten salt or hot oil) which can substantially reduce component distortion. This process is limited to selected alloy-containing steels and suitable section sizes. Austempering can be applied to thin sections of certain medium- or high-carbon steels or to alloy-containing steels of thicker section. It requires a high temperature quench and hold, usually in molten salt, and results in low distortion combined with a tough structure that requires no tempering. It is widely used for small springs and pressings.
Case Hardening
Carburising and carbonitriding are “thermochemical” treatments, usually conducted at temperatures in the range 800-940°C in the first stage of “case-hardening”. These processes change the chemical composition of the surface of a low-carbon steel component so that subsequent fast cooling, by “quenching” produces a hard “case” combined with a softer/tougher “core”.
Quenching is normally followed by a low-temperature tempering / stress relieving treatment.
In carburising, controlled levels of carbon are introduced at the surface and allowed to diffuse to a controlled depth. In carbonitriding, nitrogen is also imparted, along with the carbon, to improve case hardenability. The heat treater employs a variety of processing media to achieve these objectives, including controlled gaseous atmospheres and molten salt (“cyaniding”).
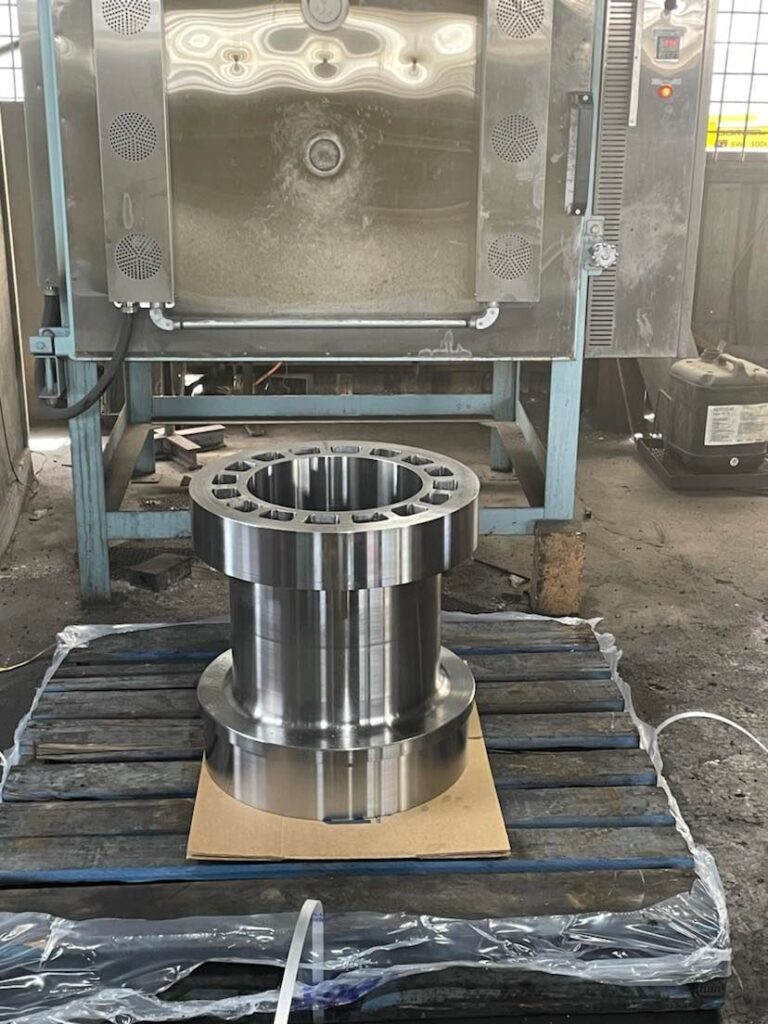

FURNACE
Furnace sizes are 900mm for Hardening and Annealing.
Aluminum and Stress Relieving has a capability of 1400mm x 1300mm Deep.
Case hardening is 800mm due to the job having to be placed into a carbonizing box.
TUFFRIDE is capable of a job being up to 700mm long.
Case Hardening
Carburising and carbonitriding are “thermochemical” treatments, usually conducted at temperatures in the range 800-940°C in the first stage of “case-hardening”. These processes change the chemical composition of the surface of a low-carbon steel component so that subsequent fast cooling, by “quenching” produces a hard “case” combined with a softer/tougher “core”.
Quenching is normally followed by a low-temperature tempering / stress relieving treatment.
In carburising, controlled levels of carbon are introduced at the surface and allowed to diffuse to a controlled depth. In carbonitriding, nitrogen is also imparted, along with the carbon, to improve case hardenability. The heat treater employs a variety of processing media to achieve these objectives, including controlled gaseous atmospheres and molten salt (“cyaniding”).
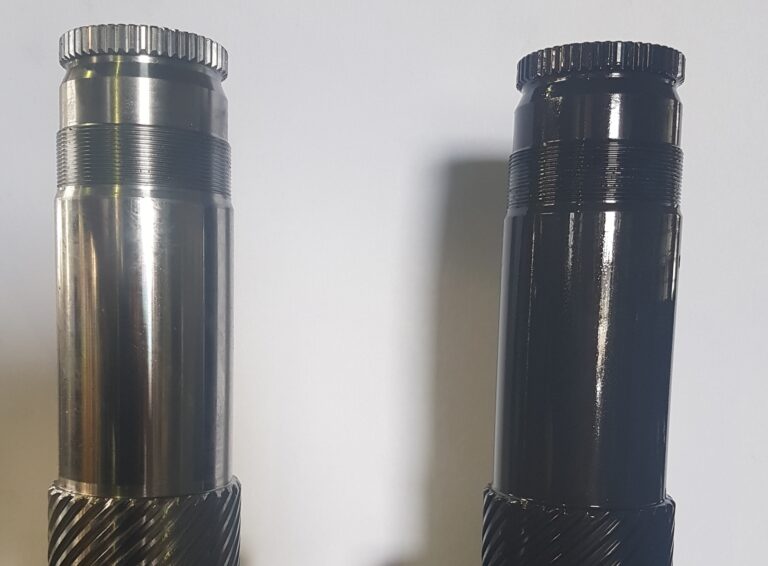